INSIGHTS
Getting More Out Of Pulsa
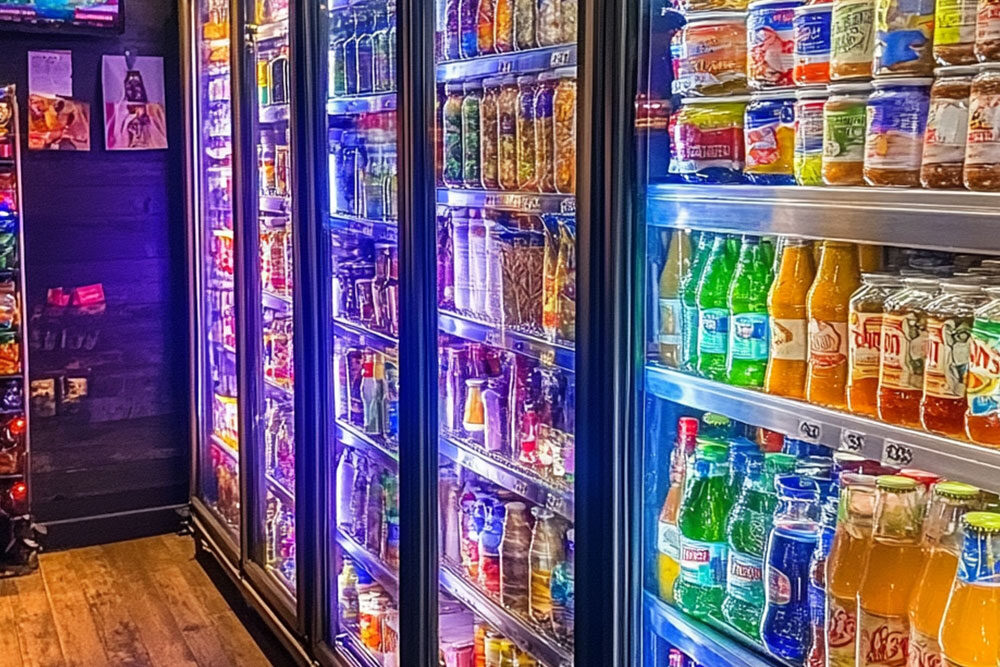
- Insights
- Why A Centralized Temperature Sensor System Is Essential For Multi-Location Restaurants
- 3 min read
Why A Centralized Temperature Sensor System Is Essential For Multi-Location Restaurants
Managing a multi-location restaurant operation is no easy feat. Balancing food safety, operational consistency, and equipment reliability while overseeing multiple units is a constant challenge. Food temperature control directly impacts safety, quality, and regulatory compliance, not to mention customer satisfaction and your business’ reputation. Relying on outdated manual checks or basic third-party sensors built into generic restaurant software often leads to missed alerts and costly oversights.
This is where a centralized temperature sensor system proves its value. It provides an online monitoring solution that allows operators to control and track temperatures across all locations on one unified platform. This system is designed specifically for the demanding conditions of food service environments. It enables quick action to prevent issues, protects perishable goods, and eliminates inefficiencies.
Why A Centralized Temperature Sensor System Matters
A centralized temperature sensor system connects individual devices across all locations. It creates a single, intuitive dashboard to manage temperature data. Unlike piecemeal solutions, this system offers a real-time view of your entire operation. This makes identifying and addressing temperature fluctuations easier before they escalate into larger problems.
Real-time monitoring is necessary in the fast-paced restaurant industry. Temperature-sensitive goods like meats, dairy, and prepped ingredients require tight control to maintain food safety and quality. With a centralized system, you can monitor all equipment—refrigerators, freezers, beverage lines, and more—from any device. This eliminates guesswork and reduces the burden on staff, who no longer need to conduct manual checks prone to human error.
Restaurants using Pulsa temperature sensors benefit from precision-engineered technology designed for the most challenging environments. These sensors operate accurately and consistently, even in walk-in freezers or fluctuating ambient temperatures in busy kitchens. The system detects deviations and provides instant notifications for swift action.
Real-Time Alerts: Prevent Problems Before They Escalate
Time is of the essence when refrigeration systems fail or temperatures deviate from safe ranges. A delay of even a few hours can lead to significant losses. Traditional methods are reactive and leave operators vulnerable to unexpected equipment failures. That’s why you need something proactive, like a temperature sensor device from Pulsa.
A centralized temperature sensor system acts as a safety net, delivering instant alerts whenever a problem occurs. For instance, if a freezer’s internal temperature rises due to a malfunction, the system immediately notifies the manager. With this real-time insight, corrective action can be taken before the inventory is compromised.
Then there’s the proactive element; real-time alerts are valuable for detecting trends that indicate potential issues. A gradual temperature increase might indicate a failing compressor or a door seal needing replacing. Addressing these problems early reduces the risk of downtime and avoids costly emergency repairs.
Boosting Efficiency Across Multiple Locations
Managing temperatures manually across multiple units is inefficient and inconsistent. Multi-location restaurant operators need a solution that scales with their business while maintaining uniform standards. A centralized temperature sensor system simplifies this process by centralizing data and providing actionable insights for every location.
Managers can review performance trends, compare equipment efficiency across units, and identify outliers with a single platform. If one location consistently experiences higher refrigeration energy consumption, the data might reveal underlying issues such as improper equipment calibration or frequent door openings. Operators can then address these inefficiencies to save costs and reduce environmental impact.
Furthermore, the system optimizes staff time. Manual checks and paperwork are replaced with automated data collection and reporting. This lets staff focus on customer service and kitchen operations rather than routine temperature logging.
Simplifying Food Safety Compliance
Health inspections are central to restaurant management but preparing for them can be stressful. A centralized temperature sensor system simplifies compliance by automating temperature logging and providing detailed records.
State and local regulations often require consistent temperature records for perishable goods and storage units. Manual record-keeping can lead to discrepancies and incomplete logs, but a centralized system eliminates this risk. The system logs data automatically to provide an accurate and reliable historical record.
Scaling Operations Without Losing Control
Expanding a restaurant chain introduces new challenges, especially regarding maintaining consistency. A centralized temperature sensor system supports growth by providing a scalable solution. New locations can easily integrate into the existing system to maintain the same high standards across all units.
The unified platform offers visibility into every location. It allows operators to spot trends, detect anomalies, and share best practices. This is particularly valuable when rolling out new equipment or standardizing procedures.
Operators retain control over their operations as the system grows without increasing administrative burdens. Staff at each location also benefit from the same level of support. This creates a smoother and more reliable operation as the chain expands.
Making a Smart Choice with Pulsa
Pulsa specializes in providing multi-location restaurants with the tools they need to achieve operational success. Our Pulsa Temperature sensors offer accuracy and reliability; they are designed specifically for the demanding conditions of food service environments. From walk-in refrigerators to beverage lines, our sensors deliver real-time data that supports operators in making informed decisions. The sensors connect seamlessly to the Pulsa Gateway, an industrial-grade communications device that transmits precision measurements to the Pulsa Dashboard every three minutes, ensuring reliable performance in any environment.
Learn how Pulsa can enhance your operations and protect your bottom line. Contact us today to explore the possibilities.