INSIGHTS
Getting More Out Of Pulsa
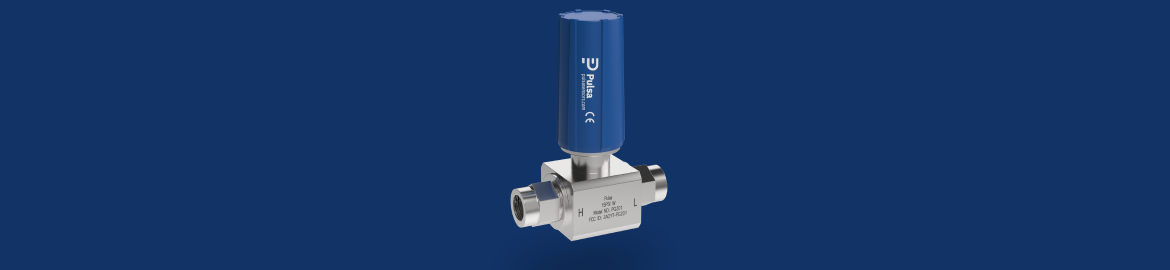
- Insights
- What Is A Differential Pressure Sensor And How It Can Save The Day
- Equipment & Supplies
- Operations
- Food & Beverage
- 5 min read
What Is A Differential Pressure Sensor And How It Can Save The Day
When it comes to measuring inventory, like a CO2 tank at a restaurant, the need for precision, efficiency, and safety is non-negotiable. Every component, from the smallest gauge to the largest tank, is central to creating a smooth flow of processes and results. Yet, one important element often stays in the background until it’s needed most: the differential pressure sensor.
Knowing what a differential pressure sensor is and how it can "save the day" for various industries opens the door to better management and optimization. It’s a tool for companies working with gas, liquid, and other materials in enclosed systems.
So, what is a differential pressure sensor, and how does it keep your systems safe and responsive? From the vast beverage tanks in bustling restaurants to the ventilation systems in high-demand facilities, differential pressure sensors provide insights that help businesses stay ahead of potential disruptions. Discover how this small but powerful sensor can be utilized across industries.
Understanding What a Differential Pressure Sensor Is
A differential pressure sensor is a specialized device that measures the pressure difference between two points. It’s a fundamental aspect for applications where maintaining balance and flow is important. These sensors detect how pressure varies between two locations in a closed system—a tank, pipe, or filter—and translate this difference into usable data. When installed correctly, differential pressure sensors offer real-time insights that help operators make informed decisions and prevent costly disruptions.
Differential pressure sensors have become invaluable across sectors, from monitoring liquid CO2 levels in large beverage tanks to assessing contamination in ventilation systems. Their applications range widely, but each use case demonstrates how this one device can make all the difference.
The Mechanics Behind a Differential Pressure Sensor
A differential pressure sensor operates through a simple yet highly effective principle. Within each sensor, a flexible diaphragm separates two chambers. Each chamber receives input from different points in the system, such as each side of a filter or two points along a pipe.
As pressure fluctuates in either chamber, the diaphragm bends accordingly. These movements can then be read as an electrical signal. This data is then interpreted to reveal the exact difference in pressure, signaling anything from a blockage to a leak. Some differential pressure sensors such as piezoresistive sensors, utilize silicon membranes for enhanced sensitivity and temperature resistance. Capacitive sensors detect pressure changes based on shifts in an internal capacitor.
This sensitive response is what makes differential pressure sensors vital in settings where accuracy is crucial. A slight shift in differential pressure can indicate potential risks, such as a leak in a closed tank.
Pictured: an exploded view of the Pulsa Differential Pressure sensor.
Common Applications of Differential Pressure Sensors
Differential pressure sensors bring stability and insight to industries where closed systems manage high volumes of gases and liquids. For companies distributing CO2 or nitrogen to the hospitality sector, these sensors monitor liquid CO2 in tanks to prevent unexpected shortages. They allow bar and restaurant owners to stay on top of their stock.
Differential pressure sensors also prove indispensable in ventilation systems, where monitoring the pressure differential across filters helps identify clogging or contamination. In the water treatment sector, differential sensors can determine water levels in large tanks, signaling when to refill or inspect for leaks. Differential pressure sensors help operators run systems smoothly by maintaining efficiency from food and beverage to manufacturing.
Pictured: A Pulsa Differential Pressure sensor and a Pulsa Pressure sensor on a CO2 tank. The sensors communicate tank levels, and alerts can be set to stay in the know. Only get alerts when needed. Know when you're running low or if there's a leak. Adding sensors is like adding a pair of eyes to a tank.
Why Differential Pressure Sensors Matter for Efficiency and Safety
Differential pressure sensors provide continuous feedback that allows operators to address problems before they escalate. In pressurized environments, any imbalance could interrupt processes or pose safety risks. Real-time monitoring can reveal these disruptions early on, such as a blockage or leakage.
For instance, in environments where liquid CO2 is central to operations, differential pressure sensors reveal whether levels are stable or depleting. If pressure levels shift unexpectedly, it could indicate a leak or other issue that needs immediate attention.
The benefits extend to industries where flow rate is key—monitoring differential pressure in a pipe helps detect obstructions, keeping production flowing smoothly.
Choosing the Right Differential Pressure Sensor
When selecting a differential pressure sensor, consider your industry's and application's specific needs. Not all sensors perform equally under varying conditions. Piezoresistive sensors are highly sensitive and resistant to temperature changes. Hence, they are more suitable for industries requiring precise measurements. On the other hand, capacitive sensors are often preferred in settings where a quick response to pressure changes is needed.
For CO2 monitoring in the beverage industry, where tank levels must be precise to avoid interruptions, a highly responsive sensor focusing on accuracy is key. The right sensor type depends on the measurement environment, whether it’s a liquid in a tank, a ventilation system filter, or a pipeline flow rate.
Integrating a sensor that aligns with your industry's physical and chemical demands will guarantee accuracy and longevity. Businesses can achieve dependable monitoring tailored to their requirements by working with a trusted provider.
Advanced Applications of Differential Pressure Sensors
In addition to traditional uses, differential pressure sensors are advancing into more complex applications. They change how industries approach safety, energy efficiency, and environmental compliance. Beyond simple tank monitoring or flow control, these sensors now provide insights that enable businesses to improve operations on multiple fronts. Here’s a closer look at some advanced uses of differential pressure sensors and how they enhance efficiency and safety in highly specialized industries.
Cleanroom Standards in Pharmaceuticals and Electronics Manufacturing
Maintaining sterile and controlled environments is essential in fields like pharmaceuticals and semiconductor manufacturing. Even slight dust, microbes, or humidity contamination can compromise product quality or render entire batches unusable. Differential pressure sensors are integral in maintaining these clean environments by controlling airflow and pressure in cleanrooms.
To prevent contamination, these cleanrooms are pressurized, typically using slight positive pressure. This guarantees that the air flows outward when doors open rather than allowing contaminants to drift in.
Differential pressure sensors continuously monitor pressure inside and outside these rooms to maintain a stable environment. This controlled environment helps companies avoid costly contamination events, maintain compliance with regulatory standards, and uphold product quality.
Optimizing Energy Efficiency in HVAC Systems
Heating, ventilation, and air conditioning (HVAC) systems are notoriously energy-intensive. As companies strive for greener, more efficient practices, the role of differential pressure sensors in HVAC optimization has become more prominent. These sensors monitor airflow and detect blockages or inefficiencies in ducts and filters.
Tracking the differential pressure across filters allows facility managers to know exactly when filters need to be replaced. This method is more effective than relying on a fixed schedule that may lead to unnecessary replacements or missed maintenance.
When filters are clogged, fans must work harder to push air through, resulting in higher energy consumption. Monitoring differential pressure helps make sure that filters are only replaced when they begin to restrict airflow. The energy savings from this alone can be substantial, particularly in large facilities or industries with constant HVAC usage.
Preventative Insights with Differential Pressure Sensors
Differential pressure sensors provide preventative insights that help companies take control of maintenance schedules and operational flows. This proactive approach is particularly useful for industries where contamination, leaks, or blockages could significantly impact production.
In facilities that rely on consistent CO2 or nitrogen levels, real-time alerts from a differential pressure sensor allow operators to prevent downtime. Additionally, monitoring the pressure differential across filters in HVAC systems makes it easy to schedule filter replacements before clogging affects air quality.
Moreover, tank monitoring provides early warning for leaks or depletion, helping companies respond quickly to preserve product quality and safety. The ability to predict issues and intervene proactively makes differential pressure sensors a powerful ally in today’s data-driven industries.
The Pulsa Advantage for Differential Pressure Sensors
Pulsa strives to deliver advanced sensor solutions that help industries manage their processes confidently. Unlike generic solutions, the Pulsa Differential Pressure Sensor and Pulsa Pressure Sensor are purpose-built to cater to the needs of companies that depend on accurate, real-time monitoring to maintain operational integrity.
Pulsa sensors were designed and built with the Pulsa platform to give operators complete visibility and control over liquid CO2 levels, flow rates, and other key metrics, sending real-time data every three minutes. This feature is unmatched by our competitors and keeps our clients fully informed about their operations. With a dedicated support team, Pulsa is committed to delivering reliable, responsive assistance whenever needed.
When every second counts, the right differential pressure sensor can safeguard your systems, products, and reputation. Reach out to our team today to discover how Pulsa can provide operational security.